The ASTEC software system
The ASTEC (Accident Source Term Evaluation Code) software system simulates all the phenomena involved in a core meltdown accident in a water-cooled reactor, from the initiating event to the release of radioactive products (known as the "source term") outside the containment [1]. This covers western-design pressurized water reactors (PWRs) such as those in France, Russian-design PWRs (VVERs), boiling water reactors (BWRs), spent fuel pools (SFP) and small modular reactors (SMR). ASTEC has also been extended to model possible accidents in the future ITER fusion facility under construction at Cadarache and the ORANO fuel reprocessing facilities at La Hague. ASTEC is maintained and developed by IRSN.
ASTEC applications mainly concern the safety analysis of nuclear installations (for example, the EPR – European Pressurized Reactor-), the assessment of the source term in accidental situations and severe accident management procedures [2]. ASTEC is used extensively to carry out IRSN level 2 probabilistic safety assessments (PSA) on French fleet and fuel cycle laboratories/plants. In addition, it is used to prepare and interpret experimental programs related to core meltdown accidents and to prepare emergency exercises (simulation exercises of a major nuclear or radiological accident to train the various stakeholders and the organization between them) of the IRSN Crisis Technical Centre.
ASTEC is the European reference software in the European Commission’s Severe Accident Research Network of Excellence (SARNET). It is also used in non-European countries (Canada, China, India, Singapore, Ukraine, South Korea, etc.).
-
-
Presentation
-
Plaquette
Organisation
ASTEC models all the physical phenomena that occur during a core meltdown accident, except steam explosion (which is handled by IRSN software MC3D) and the mechanical strength of the containment (which is handled at IRSN by CEA software CAST3M).
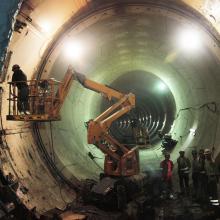
Main models
Each module (described in details in [3] and [4]) deals with the phenomena involved in one part of the reactor or one phase of the accident, and in particular:
- Two-phase thermal-hydraulics, to represent coolant flows in the primary and secondary circuits, with a two-dimensional approach in the reactor vessel
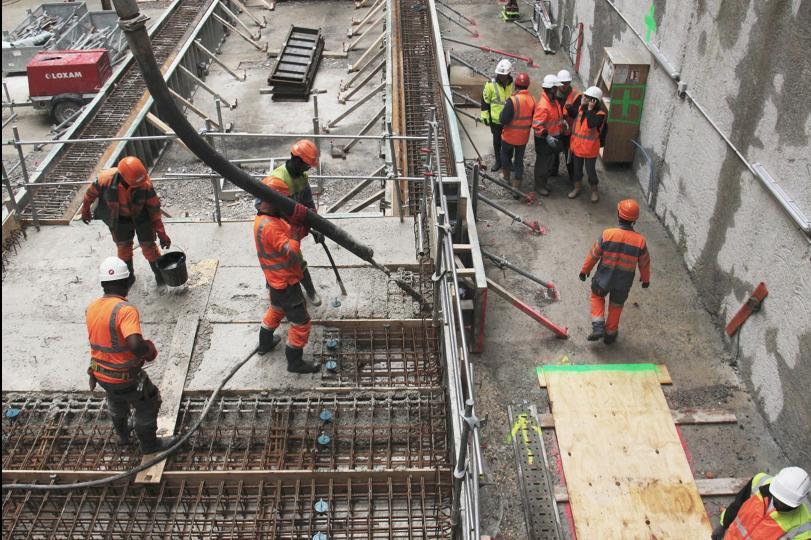
- Degradation of materials inside the vessel, when temperatures reached under the effect of the core decay heat exceed a threshold leading to significant oxidation of the cladding by steam, as well as various chemical interactions between materials making up either the fuel rods or the control rods. This can lead to the melting of materials, resulting in the formation of a mixture of molten materials known as "corium". It can also result in the formation of solid debris from the pre-fracturing of the fuel pellets combined with the embrittlement of the fuel cladding. The behaviour of the corium once located in the reactor vessel lower head is modelled until the possible lower head rupture or corium stabilization inside the vessel in case of external cooling of the vessel
- The release of Fission Products (FP), in particular iodine, from the core fuel, whether still in place inside the cladding or relocated in the form of debris or corium
- The transport of FP and aerosols and their physico-chemical behaviour in the primary and secondary circuits, then in the containment. Particular attention is paid to the behaviour of the many iodine species in their various forms (molecular iodine, gaseous organic iodides, iodine oxides in aerosol form, etc.)
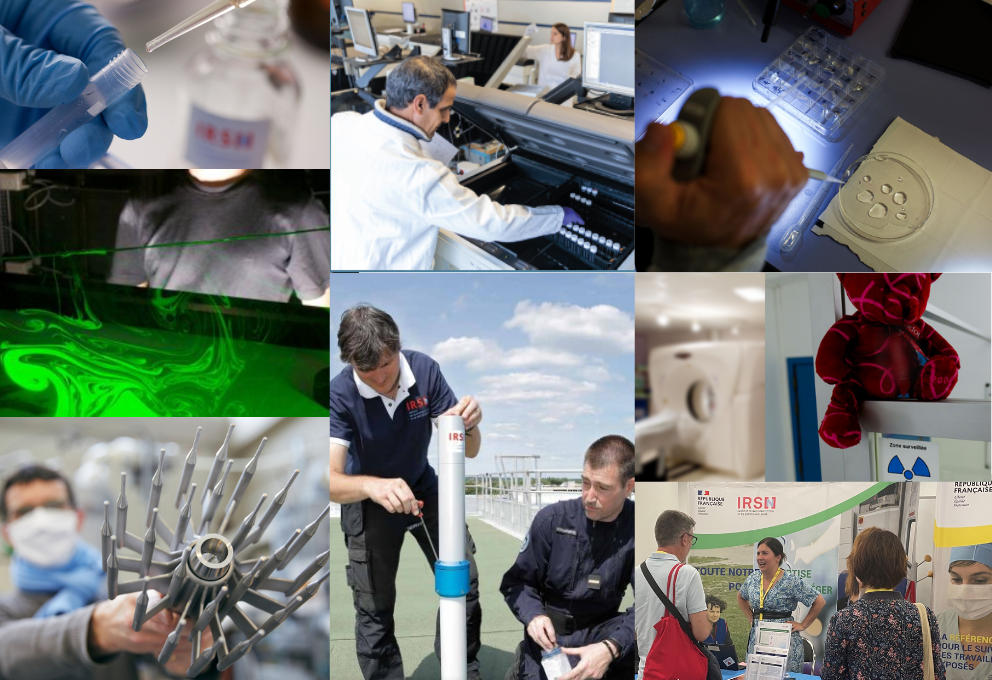
- Thermal-hydraulics in the containment, using a 0D volume approach known as "lumped parameter code"
- The erosion of the vessel pit floor by the corium located there in the event of a vessel rupture, taking into account any secondary pouring (delayed relocation of corium into the vessel pit as a result of the vessel emptying through a breach that propagates down the vessel). This erosion, known as molten corium-concrete interaction (MCCI), is modelled using a one-dimensional volume or layer approach. The model can be used to deal with dry or wet MCCI conditions, the latter including the cooling of corium by flooding under water in accordance with severe accident management procedures
Other models and functions
ASTEC also deals with other physical phenomena likely to occur during the accident, such as:
- Direct Containment Heating (DCH) due to the transfer of corium and hot gases to the walls of the vessel shaft after the vessel rupture
- Combustion of the hydrogen and carbon monoxide accumulated in the containment and the associated risk of detonation or deflagration
In addition, ASTEC assesses the isotope activity at each point in the simulated accident transient and calculates the associated residual power in any zone of the reactor.
ASTEC models evolve to follow the state-of-the art. With regard to the behaviour of fission products in particular, a large part of the knowledge has been acquired through the interpretation of tests carried out as part of the Phébus and ISTP programs, followed by the OECD/NEA STEM/STEM2 projects. As regards 3rd generation reactors (Gen III and III+), specific models simulate the corium spreader of the EPR reactor. In addition, specific functionalities were integrated from versions V2.1 in order to cover the problems associated with the strategy of corium retention in the reactor vessel; these developments were carried out by IRSN as part of the European H2020 IVMR ("In-Vessel Melt Retention") project (see [8]).
Core degradation models, an essential part of ASTEC, have been greatly improved from the V2 versions family, using those of the ICARE2 mechanistic software, to which IRSN has devoted a great deal of effort since the early 1990s, particularly in connection with the Phébus CSD and Phébus PF experimental programs [5] and [6].
Validation
ASTEC validation is based on more than 300 tests performed on more than 50 different facilities worldwide, in particular:
- Analytical tests with separate or coupled effects. For example, the VERDON tests (CEA) concern the release and transport of fission products, CHIP+ (IRSN) the chemistry of aerosols in the circuit, OLHF (SNL, USA) the mechanical failure conditions of the vessel bottom, and BIP (CNL, Canada) the behaviour of iodine in the containment
- Integral tests such as Phébus PF (IRSN), which simulates an entire accident using real materials, right up to the source term in the containment, or QUENCH (KIT, Germany), which represents the degradation of a rodbundle in simulating materials, or CCI (ANL, USA), which deals with corium-concrete interaction
Among these 300 tests, most of the OECD/NEA ISP (International Standard Problem) exercises have been selected because they are international references due to the high quality of their measurements and their use for benchmarks between software (PACTEL, VANAM, BETHSY, LOFT tests, etc.). In addition, ASTEC validation matrix is continually enriched by current international programs: OECD-ROSAU (Argonne National Laboratories, USA), OECD STEM/OECD STEM2 (IRSN), OECD BIP2/BIP3 (Canadian Nuclear Laboratories, Canada), OECD THAI-2/THAI-3 (Becker Technologies, Germany), etc.
For each new version of ASTEC, IRSN carries out the whole validation matrix P. Chatelard and L. Laborde “ASTEC V2.2 code validation: Illustrative results and main outcomes”, Nuclear Engineering and Design, 413 112547, ISSN 0029-5493 (2023), https://doi.org/10.1016/j.nucengdes.2023.112547. Most of IRSN international partners in the field of severe accidents contribute to this vast task of validating the software, usually as part of collaborative projects, and have done so for many years. This was the case, for example, for versions V2.1.0 and V2.1.1 as part of the CESAM project (see [7]) under the European Commission’s 7th FPRD, and more recently as part of the ASCOM project.
Finally, the software is regularly used for simulations of light water nuclear reactor accidents that have taken place around the world in order to consolidate its results before applying it to reactor configurations in production or under construction. These reactor-scale validation tasks mainly concern Unit 2 of the US Three-Mile Island reactor (TMI-2), which core partially melted in 1979, and the three accidented reactors at Fukushima-Daiichi in Japan in 2011.
Its ability to adequately simulate any core meltdown accident scenario in reactors currently in operation has greatly benefited the IRSN level 2 probabilistic safety assessments (PSA2) on 900 and 1300 Mwe PWRs. ASTEC can simulate most of safety systems and actions or procedures carried out by operators working in current reactors (depressurization of the primary circuit, spraying of the containment, reflooding of a more or less severely degraded core, recombination of hydrogen in the containment, etc.).
In addition, comparisons are regularly made with mechanistic software such as CATHARE (French reference software for the safety analysis of reactors outside severe accidents in two-phase thermal-hydraulics) in order to check that the thermal-hydraulics of the circuits during the head of the severe accident sequence are correctly assessed by ASTEC. The aim of this approach is to ensure that the initial conditions of the in-vessel degradation phase as estimated by ASTEC can be considered to be sufficiently consolidated to be able to carry out a relevant analysis of the rest of the accident sequence.
International collaborations
ASTEC is heavily involved in international projects dedicated to nuclear safety. ASTEC is used to carry out part of the calculations in European projects dedicated to the study of SMRs (Small Modular Reactors) such as PASTEL (dedicated to the study of passive systems [16]), ELSMOR [17] and more recently SASPAM-SA (link to https://snetp.eu/portfolio-items/saspam-sa/) on the mitigation of severe accidents in SMRs [18]. ASTEC is also used as a calculation tool in other European projects such as MUSA (Uncertainty and management of severe accidents [19]) or AMHYCO project (https://amhyco.eu/) concerning the risk of hydrogen explosion in the late phase of a severe accident and the means of detecting this risk.
ASTEC is also at the center of the European ASSAS project, which began in November 2022 and will run for 4 years. This project is coordinated by IRSN and brings together the scientific community involved in severe accidents, as well as organizations specializing in the numerical methods used in Artificial Intelligence (AI) and the Spanish specialist in power plant simulators (Tecnatom). The aim of this ambitious project is to create a proof of concept for a severe accident simulator based on ASTEC. To achieve this, it is planned not only to develop the graphical part of the simulator, but also to implement 'classic' optimisation techniques as well as techniques derived from AI to accelerate the calculations in order to achieve the ASTEC performance targets required for use in a simulator.
Maintenance and user support
With more than a hundred ASTEC users around the world, several engineers are permanently on hand to provide the most efficient possible support to users, with a particular focus on responding quickly to queries.
Users can easily download any new version or revision of the software, as well as any documentation, via the ASTEC web portal. In addition, this portal has a request management system to manage the exchange of information between software developers and users, in particular for anomaly reports and the solutions provided.
Training in the use of ASTEC software is also offered regularly by IRSN.
ASTEC future prospects
In terms of validation, ASTEC will continually incorporate improvements to the models, reflecting advances in R&D in the field of severe accidents. ASTEC will continue to be validated on the basis of standard OECD exercises, as well as on the basis of programs currently underway abroad, such as the OECD ESTER and THEMIS programs on Source Term aspects, and ROSAU on underwater corium-concrete interaction.
In addition, ASTEC will be enriched with models and functionalities to take into account new types of future installation such as SMRs or AMRs, new materials such as ATFs (Advanced Tolerant Fuel) or new types of installation such as fuel reprocessing facilities.
Références
[1] Chatelard P., Reinke N., Arndt S., Belon S., Cantrel L., Carénini L., Chevalier-Jabet K., Cousin F., Eckel J., Jacq F., Marchetto C., Mun C., Piar L., “ASTEC V2 severe accident integral code main features, current V2.0 modelling status, perspectives”, Nuclear Engineering and Design, 272 (June 2014), p.119-135
[2] Caroli C., Bellenfant L., Bonneville H., Phoudiah S., Chambarel J., Cozeret R., Veilly E., Raimond E. “Examples of recent and on-going reactor accident analysis with the ASTEC integral code at IRSN”, 7th European Review Meeting on Severe Accident Research (ERMSAR 2015), Marseille (France), March 24-26, 2015
[3] Chatelard P., Belon S., Bosland L., Carénini L., Coindreau O., Cousin F., Marchetto C., Nowack H., Piar L., Chailan L, “Main modelling features of ASTEC V2.1 major version”, Annals of Nuclear Energy, vol.93 (July 2016), pp.83-93
[4] Chailan L., Bentaïb A., Chatelard P., “Overview of ASTEC code and models for Evaluation of Severe Accidents in Water Cooled Reactors”, IAEA Technical Meeting on the Status and Evaluation of Severe Accident Simulation Codes for Water Cooled Reactors, Vienna (Austria), October, 9-12, 2017
[5] De Luze O., Haste T., Barrachin M., Repetto G., “Early phase fuel degradation in Phébus FP: Initiating phenomena of degradation in Phébus FP fuel bundle tests”, Annals of Nuclear Energy: Special issue on Phebus FP final seminar, Vol.61, p.23-35 (November 2013)
[6] Barrachin M., De Luze O., Haste T., Repetto G., “Late phase fuel degradation in the Phébus FP tests”, Annals of Nuclear Energy: Special issue on Phebus FP final seminar, Vol.61, p.36-53 (November 2013)
[7] Nowack H., Chatelard P., Chailan L., Hermsmeyer S., Sanchez V.H., Herranz L.E., “CESAM – Code for European Severe Accident Management, EURATOM project on ASTEC improvement”, 8th European Review Meeting on Severe Accident Research (ERMSAR 2017), Warsaw (Poland), May 16-18, 2017
[8] L. Carénini, F. Fichot, N. Bakouta, A. Filippov, R. Le Tellier, L. Viot, I. Melnikov, P. Pandazis, Main outcomes from the IVR code benchmark performed in the European IVMR project, Annals of Nuclear Energy, Volume 146, 2020, 107612, ISSN 0306-4549
[9] Bonneville H., Bentaïb A., Cousin F., “Fukushima accident computations with ASTEC: how to match the dose measurements in the environment with the simulations”, IAEA Technical Meeting on the Status and Evaluation of Severe Accident Simulation Codes for Water Cooled Reactors, Vienna (Austria), October, 9-12, 2017
[10] Chatelard P., Gabrielli F., Fichot F., Bonneville H., Bouillet C., Belon S., Chailan L., Sanchez V.H., “Contribution of ASTEC numerical simulations to the understanding of the Fukushima accidents”, IAEA Workshop on advances in understanding the progression of severe accidents in Boiling Water Reactors, Vienna (Austria), July 17-21, 2017
[11] Bonneville H., Carénini L., Barrachin M., “Core Melt Composition at Fukushima Dai-ichi: Results of Transient Simulations with ASTEC”, Nuclear Technology, Vol 196 - n°3 (December 2016), p.489-498
[12] Belon S., Bouillet C., Topin V., Bonneville H., Andrews N., “Insight of core degradation simulation in integral codes throughout ASTEC/MELCOR crosswalk comparisons and ASTEC sensitivity studies”, 8th European Review Meeting on Severe Accident Research (ERMSAR 2017), Warsaw (Poland), May 16-18, 2017
[13] Girault N., Cloarec L., Fargès B., Poumerouly S., Lebel L., Herranz L., Bandini G., Perez-Martin S., Hering W., Ammirabile L., Spengler C., Buck M., “Main outcomes from the JASMIN project: development pf ASTEC-Na for severe accident simulation in Na cooled fast reactors”, International Conference on Fast Reactors and Related Fuel Cycles: Next Generation Nuclear Systems for Sustainable Development (FR17), Yekaterinburg (Russian Federation), June 26–29, 2017
[14] Mikityuk K., Girardi E., Krepel J., Bubelis E., Fridman E., Rineiski A., Girault N., Payot F., Buligins L., Gerbeth G., Chauvin N., Latge C., Garnier J.C., “H2020 ESFR-SMART project: status after 6 months”, Nuclear Days 2018 - NUGENIA Annual Forum 2018, Prague (Czech Republic), April 10-12, 2018
[15] Chevalier-Jabet K., Mabrouk A., Baccou J., Zheng X., Maruyama Y., “Overview of recent methods for the modelling of the uncertainties on the calculation of consequences of a nuclear power plant severe accident”, 2015 International Congress on Advances in Nuclear Power Plants- ICAPP-2015), Nice (France), May 03-06, 2015
[19] MUSA – MANAGEMENT AND UNCERTAINTIES OF SEVERE ACCIDENTS (musa-h2020.eu)